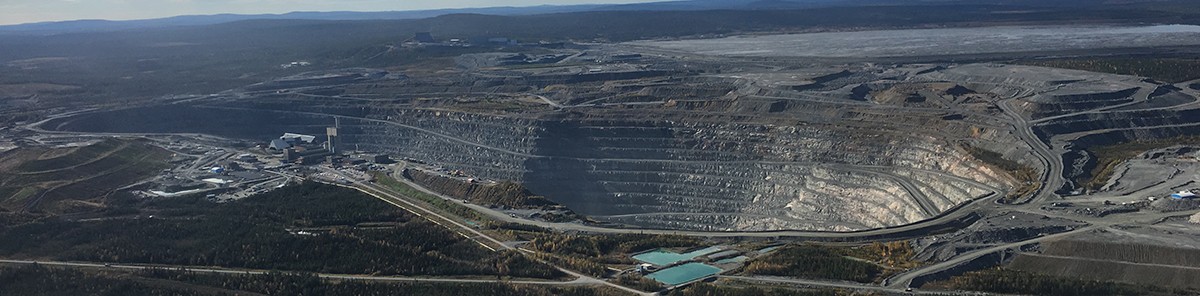
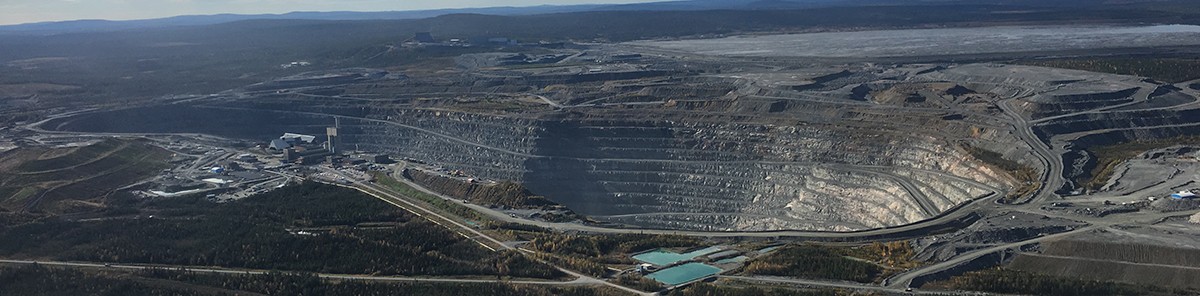
Iron ore dressing plant
Handling abrasive fluids can be tough for many industries, especially in mining. Traditional valves, like stainless steel and iron cast valves, often wear out quickly, leading to high maintenance costs. In this case, in one of the largest iron mines in Sweden, our Ramén Ball Sector Valve KSG proved that soft natural rubber in certain cases is much more resistant than steel.
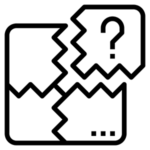
Challenge
Water leakage from the valve body caused by severe wear on the inlet cover ring, ball sector, and seat ring.
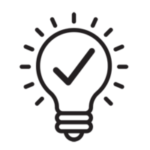
Solution
A soft rubber lined KSG ball sector valve size 150 mm.
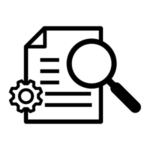
Result
No signs of wear or damage and lower maintenance costs compared to traditional valve solutions.
Application: Throttling of deposit from thickener
Flow rate: 120-240 m3/h with 10-30% solids
Grain size: about 1mm
Inlet pressure: 0,8 bar
Pressure drop: 0,8 bar
Background
Controlling abrasive fluids is known to be a challenge for any industrial applications. Each valve technology has its strengths and weaknesses, and they need to be evaluated based on the specific media being handled. Key considerations to be considered are purchase cost, installation cost, and, most critically for abrasive media, maintenance costs. Prior to the development and use of rubber lined valves, the standard solution found in mining operations handling abrasive media were stainless steel or iron cast valves. This proved to be an inefficient solution, both technically as well as financially.
Challenge
In this case as a first solution a standard stainless steel ball sector valve (size 150 mm) was installed, featuring a hard chromium faced ball sector, stellited inlet cover ring, and seat ring. Within approximately 40 days of installation, inspections revealed water leaking through the valve body due to significant wear on the inlet cover ring, ball sector, and seat ring.
Measures and Results
To address the wear issues, a soft natural rubber lined valve (size 150 mm) was installed in the same application. After six months, with four months of continuous service, the valve was inspected, revealing no signs of wear or damage. The customer had tested several other valve technologies, such as rubber pinch valves and lined butterfly valves in the same service and none had lasted more than two months. Changing to Ramén KSG rubber lined ball sector valves gave the customer several benefits including much lower maintenance cost and downtime.