Flotation Process to Separate Valuable Minerals
Flotation is a widely used process for separating valuable minerals from their ores. The method relies on the ability of certain minerals to attach to air bubbles, while other materials remain submerged in water. By adding specific chemicals known as reagents, the process can be optimized to improve the recovery and grade of valuable minerals.
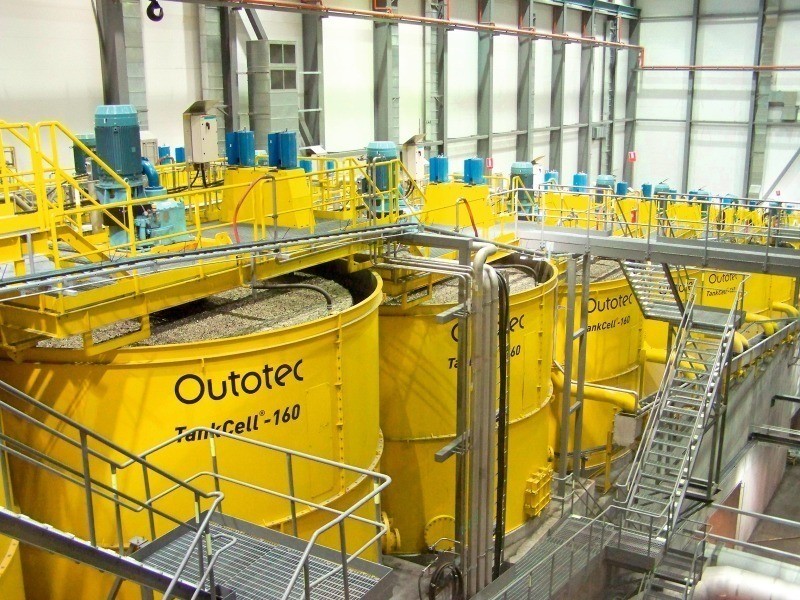
Background
Other common methods for mineral separation include gravity separation, magnetic separation, and leaching. Each of these methods has specific applications depending on the nature of the ore and the target minerals. However, flotation remains particularly effective for sulfide ores and complex mineral compositions.
The flotation process involves several key steps, including ore preparation, reagent addition, air introduction, froth collection, and final concentration of the minerals. Each step is crucial in ensuring the effectiveness and efficiency of the flotation process.
1. Ore Preparation
The raw ore is crushed and ground to a fine size to liberate the valuable minerals from the surrounding material.
2. Reagent Addition
Collectors: Chemicals that promote hydrophobicity in the target minerals, enabling their attachment to air bubbles.
Frothers: Help in the formation of stable bubbles that can carry the hydrophobic minerals.
Depressants: Prevent certain minerals from attaching to the bubbles.
Activators: Increase the likelihood that certain minerals will attach to the bubbles.
pH Modifiers: Control the alkalinity or acidity of the slurry, optimizing conditions for flotation.
3. Air Introduction
Fine air bubbles are introduced into the slurry. The valuable minerals, which have become hydrophobic due to the collector, attach to the bubbles and rise to the surface.
4. Froth Collection
The mineral-laden froth is skimmed off the surface. This froth contains the target minerals, while the waste material, called tailings, remains in the slurry.
5. Final Concentration
The collected froth is further processed to extract the concentrated mineral product.
Key reagents used in flotation include:
- SHMP (Sodium Hexametaphosphate): Used to disperse slimes and inhibit unwanted mineral flotation.
- Xanthates: Commonly used collectors for sulfide minerals.
- Methyl Isobutyl Carbinol (MIBC): A frother that ensures the formation of a stable froth.
- pH Modifiers (e.g., lime or sulfuric acid): Adjust the pH to ensure the optimum flotation environment.
Challenge
The flotation process requires precise dosing of reagents to achieve optimal performance. The inherent corrosiveness of flotation reagents imposes significant demands on equipment, particularly valves, which must be able to withstand harsh conditions while providing accurate flow control. We provide Ramén KS Ball Sector Valves and Microflow valves from Badger Meter for dosing. Which valve type depends on the process conditions and the reagent properties:
Ramén KS Ball Sector Valves: High-capacity flow control and tight shut off, ensuring zero leakage and accurate control of high to medium flow.
Microflow globe valves, RCV: Used for precise control of low flow rates, critical when dosing expensive reagents like collectors and frothers.
Feel free to contact us for help finding the right valve for your application. You can also book a meeting directly with one of our product specialists.
Technical requirements for valves and equipment
- Corrosion Resistance: Since many flotation reagents are highly corrosive, valves and pipelines need to be constructed from materials such as stainless steel, PTFE, or ceramic linings.
- Precision: The valves must allow for fine control over reagent flow to prevent wastage and ensure that the optimal concentration is maintained in the slurry.
- Automation and Monitoring: Automated control systems with feedback loops are essential to monitor flow rates and chemical concentrations in real-time. This minimizes human error and maximizes the efficiency of the flotation process.
Result
In addressing these challenges, several mining operations have successfully optimized their flotation processes by utilizing our Badger Meter valves, which we have expertly sized and selected for these specific conditions:
- Aitik Mine (2008): The Aitik mine implemented a multi-stage flotation system to separate copper, gold, and silver. By utilizing precise reagent dosing systems, they were able to maximize mineral recovery from complex ore bodies.
- Kaunis Iron (2023): In 2023, Kaunis Iron launched an advanced flotation plant for iron ore beneficiation. Incorporating modern automation technology and optimized reagent dosing valves significantly improved the efficiency of their separation process, resulting in higher-grade iron recovery while reducing waste.
Conclusion
Flotation remains a critical method for the beneficiation of valuable minerals, especially in complex ores. The careful selection of reagents and precise control over their dosing, supported by advanced valve technology, play a vital role in maximizing the efficiency of the flotation process. Optimizing valve materials and integrating automation can greatly enhance performance, leading to improved recovery rates and higher-grade products.
Legend: Chemicals Used in Reagents
- SHMP: Sodium Hexametaphosphate
- MIBC: Methyl Isobutyl Carbinol
- Xanthates: Collectors for sulfide minerals
- Lime: pH Modifier
- Sulfuric Acid: pH Modifier
Contact us
Use the form to contact us.