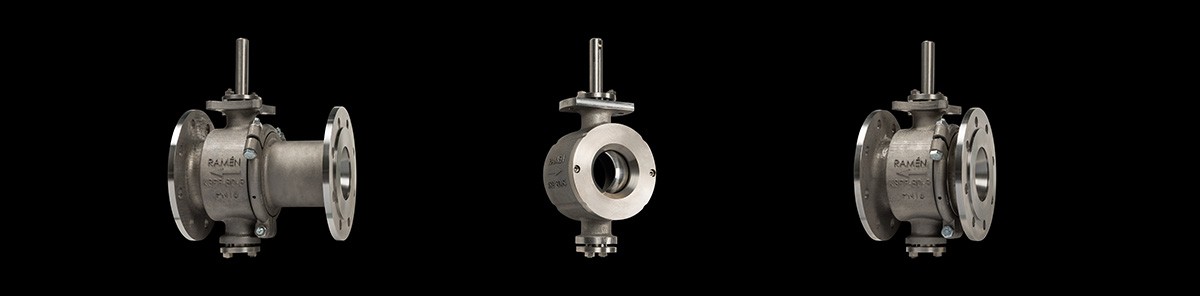
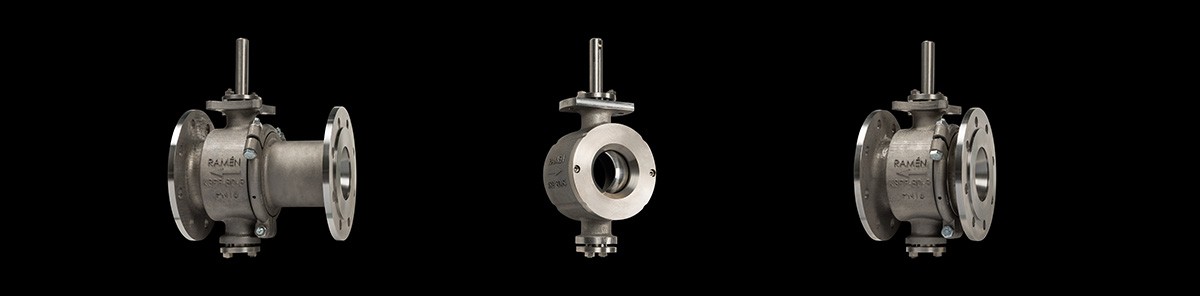
Additive manufacturing - Next generation industrial valves
Ramén Valves are one of the first valve manufacturers in the world to offer control valves in titanium grade 5 using additive manufacturing (AM). Short lead times, green technology and the speed of design are a few of the many benefits with AM technology.

What are the benefits with AM?
Short lead times
Using AM allows us to deliver a Ramén Ball Sector valve within 4 weeks from getting the order, regardless of
dimension and other characteristics. This can be compared to the more traditional methods where the lead time is up to a couple of months.
Green technology
Additive manufacturing technology builds the product in layers, reducing material waste and consumption. The waste generated in the process is reused in manufacturing and does not loose any of its properties.
Speed of design and flexibility
AM allows quick design changes without compromising pricing and the short lead times. AM is also very cost efficient for manufacturing smaller batches.
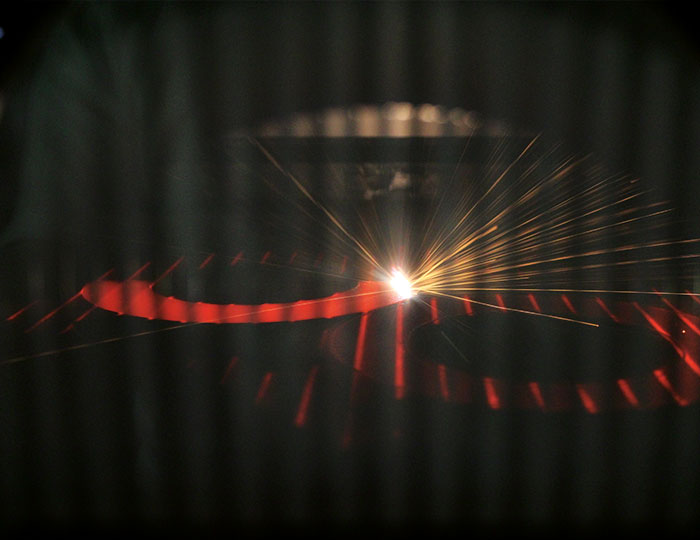
The technolgy – This is how EBM works
The method used by our supplier AIM Sweden is called EBM (Electron Beam Melting). EBM is the process of producing parts by successive melting of layers of material rather than removing material. Each layer is melted to the exact geometry defined by a 3D computer model. The process provides a solid material whose properties is better than casted material and comparable to forged material.
High power (3.000 W)
Allows for high melting capacity
High productivity
No moving parts in the EB-gun
Extremely fast & accurate beam control
Vacuum process
Clean & controlled environment
Hot process (650ºC for titanium)
No residual stresses
No heat treatment (of titanium)
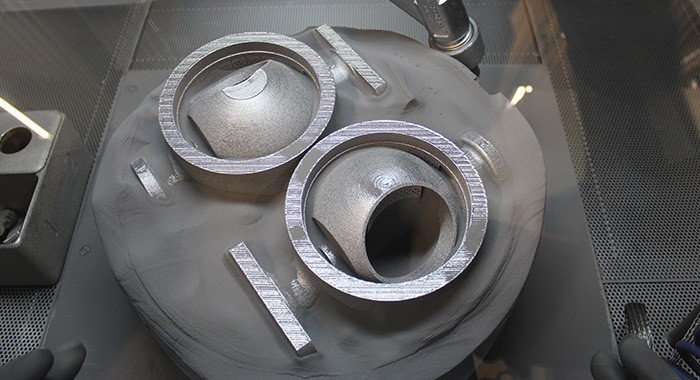
How we became a pioneer in the industry of additive manufacturing
In this article, published by G Additive, we share our journey into additive manufacturing and how it has positioned us as a pioneer in the industry.
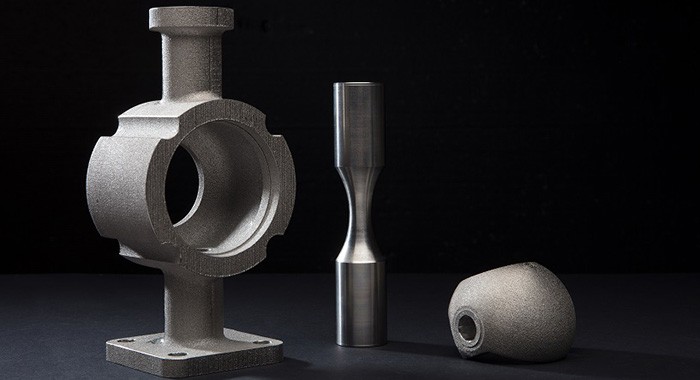
Ramén Valves featured in Easy Engineering Magazine
In this article Our CEO Per Wennersten and Sales Manager Stéphane Blanchet discussed our commitment to innovation and sustainability. The article describes how we use additive manufacturing (AM) to produce control valves in titanium grade 5.