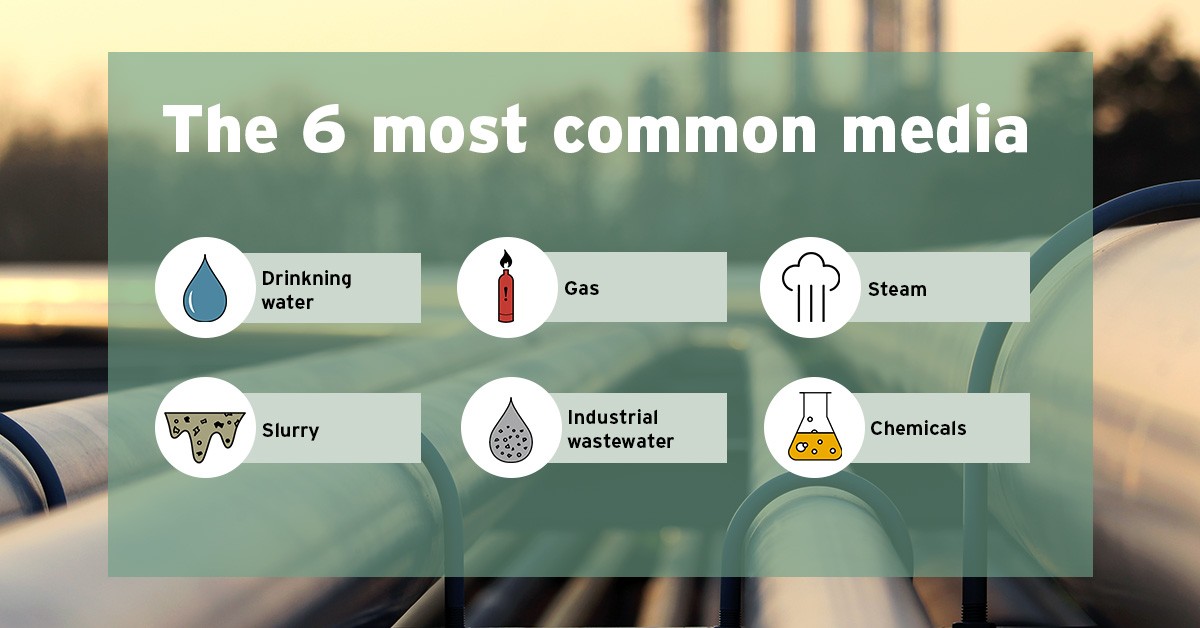
Ramén Valves, 05 June
How to choose the right valve for different media
We get a lot of questions about how to choose the right valve for different media. Unfortunately, there are no one-size-fits-all solutions when it comes to valves. The type of product you need depends largely on the media it will handle.
Therefore, we have put together a list of various factors to consider when choosing a valve for some of the most common media. In order to optimize the performance and increase the lifetime of the valves.
Here are some of the most common media:
Drinking water/Potable water
When choosing a valve for drinking water applications, it is crucial to prioritize safety, reliability, and compliance with relevant regulations. Here are some key points to keep in mind:
- Material compatibility: Select a valve made from materials that are compatible with drinking water and will not contaminate or react with the water. Commonly used materials for drinking water valves include stainless steel, brass, and food-grade plastics.
- Certifications and standards: Look for valves that comply with relevant certifications and standards for drinking water applications in your region. E.g. EC declaration 2023/2006 and 1935/2004 for EU, FDA for US.
- Valve type: Different valve types are suitable for various applications. Common valve types for drinking water include ball valves and butterfly valves.
Gas
Choosing valves for gas can sometimes be tricky since the gas is changing properties with temperature and pressure. Most importantly you need to avoid leakage and therefor select a valve that is absolutely tight when closed. For some gases this can be a challenge – for example, helium is very difficult to shut off.
But valves should not just be tight when they close (known as internal tightness). They also have to meet the relevant tightness requirements for release into the atmosphere, external tightness to avoid fugitive emissions, especially if the media is classified as flammable, explosive or harmful to the enviroment. In many cases, the standard Approval for leakage to atmosphere according to ISO 15848-1 and VDI 2440 (TA-Luft) is applied.
Primarily the valve shall be able to handle the pressure, PN class but also consider pressure drop over the valve. A valve that creates a high pressure drop will “eat up” a lot of the energy, meaning a larger compressor is required adding on costs. This means more energy consumption – and higher costs.
Steam
Steam is a complex medium to handle, and to make the most of its properties you need to pay extra attention to the temperature and pressure throughout the system. Because valves change pressure and temperature as steam passes through, the correct valve type and sizing is required. One problem that often arises is noise, which occurs at extremely high velocities in the valve.
You can limit this by making sure that the sizing is based on correct process parameters.
Slurry
Slurry, fibre suspension (e.g. paper pulp) and wastewater contain fibres or particles that can stick to the valve and block it. This is called dewatering or plugging. Make sure you have calculated the correct velocity through the valve and there are no valve parts in the way of the flow.
High flow rates can cause the particles to eat away at the valves from the inside through what is known as abrasion. By choosing the right valve that can handle velocities, you can extend its life and reduce maintenance requirements.
Industrial wastewater
Industrial wastewater is in many cases difficult to define. It can contain chemicals that can corrode the material and damage the soft parts. Often it is not clear what might be going into the pipe. The more you know about the media to be controlled, the lower the cost and the better the solution. And conversely, the less you know, the more you have to allow for all eventualities and design for the worst.
One phenomenon that can occur is cavitation. Due to process conditions, vapor bubbles are created in a fluid, which can cause damage to the valve. This creates noise, ranging from a small crackling sound to a deafening din in the working environment.
If corrosive or oxidising fluids leak down the drain, the consequences can be significant. If there is a risk of this, choose valves and other components that can cope.
Chemicals
Pure chemicals can corrode the valve to an even greater extent and damage its soft parts. Chemicals can be not only in the medium that the valve will handle, but also in the environment around the valve.
Therefore, when choosing valves for chemical processes, take your time to thoroughly assess all the important factors, such as:
- Chemical compatibility
- Temperature and pressure
- Valve type
- Valve size and flow capacity
- Actuation method
- Maintenance and reliability
- Standards and certifications
- Cost considerations
Are you developing and delivering solutions for the process industry and want to know more about which valves are best for your solution, contact us directly and we’ll help you.